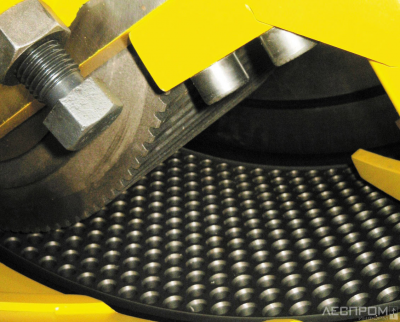
Тепловой расчет, конструкция и производственный потенциал
Пеллетирование древесины зависит от комплекса факторов. Это и характеристики сырья – порода, влажность, размер и форма частиц, и конструктивно-технологические параметры – мощность привода, диаметр пеллет, добавки и т. п.
Ввиду этого создается впечатление, что производительность прессов разных моделей объективно оценить невозможно. Тем не менее способ объективной оценки существует и позволяет сравнить прессы по удельной производительности, энергетической эффективности и производственному потенциалу.
Датские ученые еще в 2009 году исследовали влияние температуры, влажности, породы древесины и добавок на силу и энергию прессования. В частности, было установлено следующее:
- процесс прессования состоит из нескольких фаз, в которых действуют силы трения и вязкого трения;
- давление в рабочей зоне достигает 450 МПа, что соответствует высоте водяного столба 45 км (в 4–4,5 раза больше глубины Марианской впадины);
- качество экспериментальных пеллет соответствовало требованиям во всем температурном диапазоне опытов, от 60 до 160°С;
- энергозатраты составили 50 кВт·ч/т при 125°С (для сосны), без учета нагрева матрицы и КПД привода.
На основании этого исследования можно сделать несколько выводов о физике пеллетирования.
Процесс идет в широком диапазоне локальных давлений, поскольку его фазы протекают одновременно и многозонально. Из-за рельефа поверхностей матрицы и роликов (рис. 1), а именно наличия отверстий, фасок и пазов, максимальное давление достижимо в зонах с плоскими поверхностями матрицы напротив плоских поверхностей роликов. Зато на этих участках материал течет во всех доступных направлениях, обволакивает и склеивает неразрушенные частицы.
Нагрев вторичен по отношению к давлению, он является внешним проявлением работы по преодолению сил трения. Как известно, работа сил трения преобразуется в нагрев.
Эта работа прямо пропорциональна давлению, а также скорости или квадрату скорости (в зависимости от вязкости при вязком трении) взаимного перемещения компонентов процесса. И давление, и скорость определяются линейной скоростью относительного движения матрицы и роликов и количеством подаваемого сырья.
Процесс пеллетирования обычно представляют как плавление лигнина при нагреве так и его действие как связующего. Но этот взгляд ограничен: и лигнин, и целлюлоза являются полимерами аморфно-кристаллического строения и состоят из нескольких блоков, различающихся температурой плавления и течения. Оба вещества содержат легкоплавкие фракции с температурой течения около 30–40°С и ниже. Но важнее, что в зонах с высоким давлением происходит течение материала в массе, вплоть до 100%. И хотя после снятия давления тугоплавкие фракции быстро отвердевают, они также участвуют в процессе.
Качество пеллет должно обеспечиваться матрицей, а именно калибрующей длиной пресс-каналов, в которых создается необходимое трение для уплотнения пеллет (фаза трения). То есть калибрующая часть пресс-каналов зависит от рабочей температуры: чем она выше, тем каналы длиннее. Несоответствие матрицы тепловому режиму или параметрам сырья компенсируется клеящими добавками.
Тепловой расчет
Поскольку внешний нагрев в оборудовании отсутствует, все энергозатраты процесса обеспечиваются приводом и выражаются количеством выделенного тепла. Тепловой расчет показывает, сколько сырья можно нагреть до рабочей температуры Траб.
Из практики известно, что пеллетные прессы разной конструкции работают в температурном диапазоне 85–145°С для сосны. Возьмем для сравнения два пресса с полярными значениями Траб (рис. 2): низкотемпературный – НТ (Траб = 85–95°С, расчетная температура 90°С) и высокотемпературный – ВТ (Траб ≤ 145°С, расчетная температура 125°С).
Требуемые исходные данные для расчета:
- количество энергии от электропривода (для обоих типов прессов применяются моторы одинаковой мощности по 355 кВт);
- конечная температура процесса (расчетная Траб для сосны);
- начальная температура про¬- цесса;
- удельная теплоемкость компонентов сырья – абсолютно сухой древесины и воды, а также металла матрицы и роликов – частей, непосредственно участвующих в процессе (рис. 3).
От этих компонентов нагреваются другие части оборудования и окружающая среда.
Сырье поступает в обработку из смесителя, который расположен выше и нагревается от рабочей зоны. Температура в смесителе принимается 65°С, это начальная температура процесса.
Потеря сырьем влаги из-за испарения выражается энергией фазового перехода «вода – пар». На практике сушка обычно составляет от 2% внутри пресса.
В расчете сушка была принята для обоих прессов 2,27%, что привело в полное соответствие результаты расчета и эксперимента: расчетная удельная энергоемкость 50 кВт·ч/т соответствует условиям эксперимента для ВТ пресса (табл. 1).
На практике следует учитывать КПД привода и ряд других факторов: коэффициент загрузки Кз, показывающий нагрузку на двигатель, охлаждение роликов (для ВТ пресса), добавку воды или пара (табл. 2).
Плавность работы пресса фундаментально зависит от его конструкции, в том числе количества роликов, что будет показано ниже. Дополнительно плавность обеспечивается Кз, который устанавливается ниже значения, за которым могут возникнуть вибрации. Для данного анализа примем Кз = 0,6, как рекомендуемый для ВТ пресса.
Охлаждение роликов вт пресса и его эффективность
Повышенная температура вредна как для пеллетизации, так и для эксплуатации пресса. Главной задачей охлаждения является улучшение условий эксплуатации оборудования: исключение избыточных износа движущихся частей и расхода смазки роликов. Физический смысл охлаждения заключается в переносе излишков тепла из рабочей зоны в холодильник, при этом излишнее тепло продолжает вырабатывается и составляет больше 50%.
С точки зрения теплового баланса тоже есть положительный эффект, однако согласно тепловому расчету он составляет всего 5,81% при снижении температуры на 35°С. И это без учета затрат на работу системы охлаждения, мощность которой 1,8 кВт. Причиной положительного эффекта является рост теплоемкости древесины с повышением температуры. А система охлаждения отводит тепло при более низкой температуре (рис. 3).
Важно отметить, что эффективность охлаждения роликов определяется для того же ВТ пресса, но без системы охлаждения.
Добавка воды и пара
Вода играет роль смазки: с повышением влажности сырья сила прессования падает. Однако на нагрев воды тратится дополнительная энергия, увеличивается и объем сушки. Независимо от начальной температуры вода подогревается сначала в смесителе вместе с исходным сырьем, а потом в рабочей зоне до рабочей температуры. Из-за высокой теплоемкости вода оказывает сильное влияние на тепловой баланс.
Добавка 5% воды снижает расчетную производительность НТ пресса (без учета сушки) на 4,7%, ВТ пресса – на 6,2%.
Добавка 5% пара, напротив, повышает расчетную производительность НТ пресса (без учета конденсации) на 9–12%, ВТ пресса – на 5–7%. Диапазоны значений зависят от начальной температуры пара – 140 или 160°С.
Если испарение воды (переход «вода – пар») требует дополнительной энергии, то при конденсации пара энергия выделяется. Однако оценить потери пара и долю конденсации не представляется возможным. На практике повышение производительности аналога НТ пресса с Траб = 105°С составляло 20%, при исключении отрицательного эффекта от предыдущей добавки воды. При более низкой Траб эффект от добавления энергии посредством пара может быть выше.
Количество роликов и вибрация
Влияние количества роликов на рабочую температуру и энергоэффективность мы ранее рассматривали (см. ЛПИ. №3 (165) за 2022 г.). Однако есть еще один аспект прямого влияния на производительность.
Иногда специально для обработки древесины используются три прессующих ролика, а не два, как обычно в прессах с круглой матрицей. Насколько рационально такое решение?
Типовая конструкция таких прессов представляет собой неподвижную ось, к которой прикреплена плита с роликами и на которой вращается главный вал привода с матрицей (рис. 4).
На схеме прессования (рис. 6) видно, что при подаче материала на роликах возникают вращающие моменты М и силы прессования F. Вместе они вызывают сгибающие моменты главной оси.
Никогда сырье не распределится таким образом, что эти моменты становятся равными. А любое их неравенство вызывает взаимные циклические смещения роликов и матрицы – вибрации. Наиболее подвержены вибрациям и восприимчивы к силовому воздействию двухроликовые системы.
Если в плоскости, проходящей через оси роликов, такая система ограничена в смещении матрицей, то в перпендикулярной плоскости – только жесткостью главной оси и главного подшипника, которые принимают на себя основные нагрузки. Действующие силы настолько велики, что могут вызвать даже излом оси или разрушение матрицы (рис. 5).
Для таких систем критична своевременная замена подшипников главного вала. Не менее важны и правильно выставленные зазоры между роликами и матрицей.
Отличие трехроликовых систем (рис. 7) – взаимное уравновешивание сгибающих сил и смещений от них во всех направлениях, что практически исключает вибрации. Смещения ограничены матрицей, и при правильно выставленных зазорах ось и главный подшипник не испытывают перегрузок, поэтому их ресурс значительно, в разы, повышается.
Кроме того, некоторые двухроликовые прессы отличает эллиптическая форма матрицы, а зазор выставляется до одного или более касаний роликов при ее провороте. Это означает, что зазоры в разных точках окружности матрицы будут различаться.
Матрица трехроликовых прессов всегда с круглым профилем, зазоры одинаковые и выставляются по щупу.
Для предотвращения вибрации в двухроликовых прессах на практике снижают нагрузку на главный привод (коэффициент загрузки Кз). Более того, для некоторых моделей проектируется недостаточная мощность подачи сырья: при стопроцентной скорости вращения питающего шнека. Кз не должен превысить 80%. А рекомендуемый Кз еще ниже – 60%. При подаче 85% нагрузка двигателя составляет 62%, у другого пресса – 75 и 57% соответственно (рис. 3). Иначе при стопроцентной подаче будет Кз ≤ 76%.
В трехроликовых прессах наоборот: задается нагрузка главного мотора до 100%, а подача материала регулируется автоматически, причем мощность подачи избыточная.
Потенциал прессов
Рабочие параметры и производственный потенциал пеллетных прессов определяются их конструкцией, которая обеспечивает специфическую температуру и плавность процесса и даже иногда требует ограничений. Например, в НТ прессе температура процесса самоограничивается 105°С (не требуется контроль автоматикой!), а в ВТ прессе она может превысить допустимую, поэтому автоматикой предусматривается останов пресса по достижении 180°С.
В контексте перспективного развития производители работают прежде всего над увеличением мощности привода. Однако на данный момент мощность привода ВТ пресса 355 кВт используется не в полной мере и с низким КПД.
Увеличение мощности НТ пресса более перспективно. Уже эксплуатируются прессы для комбикорма мощностью 400 кВт. Также актуальна реализация потенциала привода 355 кВт для древесины за счет технологического обеспечения постоянного высокого Кз двигателя или добавки внешней энергии в виде пара.
Эти выводы подтверждаются экспериментами, расчетом и практическими данными производителей и эксплуатантов прессов. По статистике НТ прессы с двигателем 355 кВт обеспечивают среднюю практическую производительность на сосне не менее 4,5 т/ч, то есть 36 тыс. т (8000 ч) в год. Для сравнения: годовая производительность ВТ пресса заявляется 30 тыс. т, что предполагает среднюю производительность не более 4 т/ч (табл. 3).
Особенности трехроликовых НТ прессов:
- минимизируют возможность вибраций, использование мощности привода не ограничивается вплоть до 100%;
- позволяют снизить скорость прессования и удельные энергозатраты;
- не требуют охлаждения роликов;
- использование трех роликов вместо двух не повышает эксплуатационные затраты, так как их износ зависит от количества произведенной продукции на каждый ролик.
Эти особенности в сочетании с другими конструктивными решениями создают условия для повышения удельной производи¬тельности прессов и снижения затрат на их обслуживание (см. табл. 3).
Текст
Виктор Анисимов, Wood&Pellet Project
Сушильные камеры для дерева различаются по типу конструкции, принципу работы и функциональности. Вот основные виды сушильных камер, используемых в деревообрабатывающей промышленности:
- Воздушные сушильные камеры
- Вакуумные сушильные камеры
- Туннельные сушильные камеры
- Контейнерные сушильные камеры
- Сушильные камеры с осушением конденсацией
- Сушильные камеры с инфракрасным обогревом
- Комбинированные сушильные камеры
Каждый тип сушильной камеры имеет свои преимущества и области применения, и выбор подходящего оборудования зависит от требований к процессу сушки, типа древесины и объема производства.